Users and future buyers of wooden windows have a common traditional belief that window surface coating needs to be repaired or re-painted for the first time in a couple of years, and then again every few years, until the windows are ready to be replaced with either new wooden windows or of other material. In most cases such belief turns out to be unjustified and unnecessary. Fears and concerns arise from the experience with wooden windows, which have been coated with thick opaque lacquers decades ago. Although they provided good water repellency, they exhibited low vapour permeability, which was also their biggest weakness. When exposed to weather conditions, erosion of the coating and cracking occurred due to the fragility and consequently the penetration of water under the coating. High wood moisture caused a lot of problems in the form of bubbles, rot of wood and peel-off the coating. Today’s coatings are fundamentally different and the development has rapidly advanced. We usually talk about lasures which ensure a long lifetime of wooden windows if appropriate quality of coating materials and formulations, and suitable application in production are provided.
1. Quality of the coating
Without a doubt, the lifetime of coating depends largely on the quality of the coating, for which the more appropriate term would be the coating system. The term coating system is used because coating consists of more than one layer and thus forms a coating system. In this paper, however, we will use the term coating for the coating system. It is therefore very important that the coating consists of several layers and at least three layers are recommended. One of the basic layers is a layer that hardens and prepares the wood surface for further layers, reduces water absorption and prevents the wood against blue stain fungi and soft rot. The second layer represents the base layer, which can be more or less pigmented, is the basis for the final layer and has a significant influence on both, the visual appearance and on the final quality of the coating. The last layer closes the surface of the wood and provides long-lasting protection against water penetration and UV radiation, which affects the thinning of the coating throughout the years and consequently the lifetime of the coating. In the case of wooden windows made of e.g. larch or oak there is necessarily to use an additional layer which prevents the oozing of resin or bleeding of extractives (e.g. tannin).
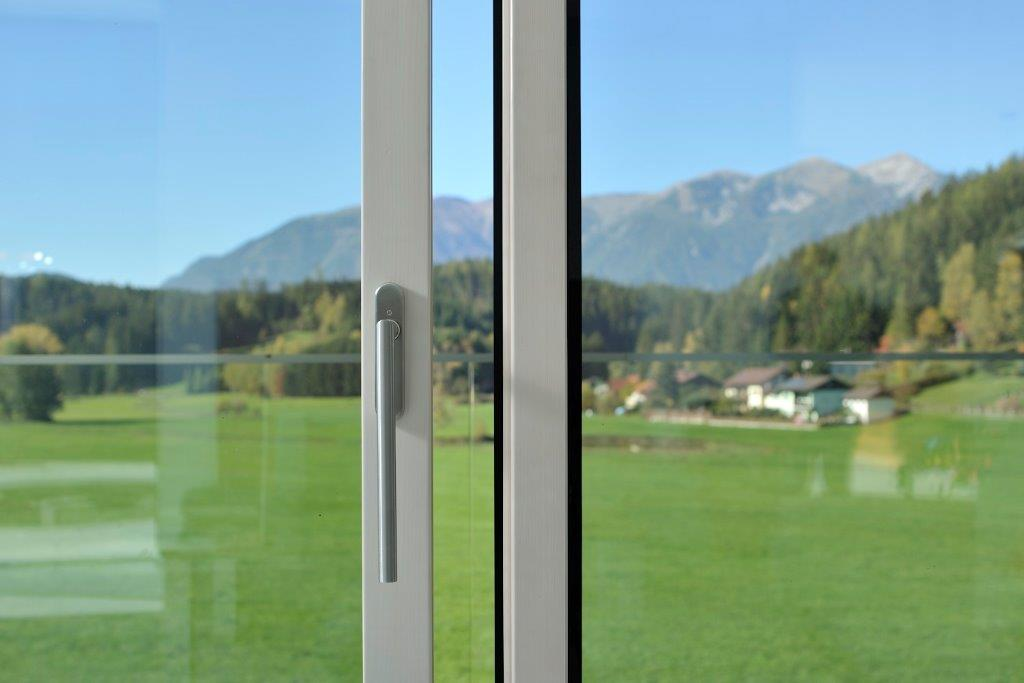
Modern coatings ensure the long lifetime of wooden windows with the appropriate quality of coating materials and formulations and suitable application in production
Significant deviations in the quality and durability of “lasure” (orange-brown hue, texture of the wood is clearly visible) and “opaque” (white hue, RAL 9016, the texture of the wood is not visible) coatings were detected in an extensive study involving 8 domestic and international producers of industrial wooden window coatings. Coatings of all producers applied on spruce wood consisted of three layers.
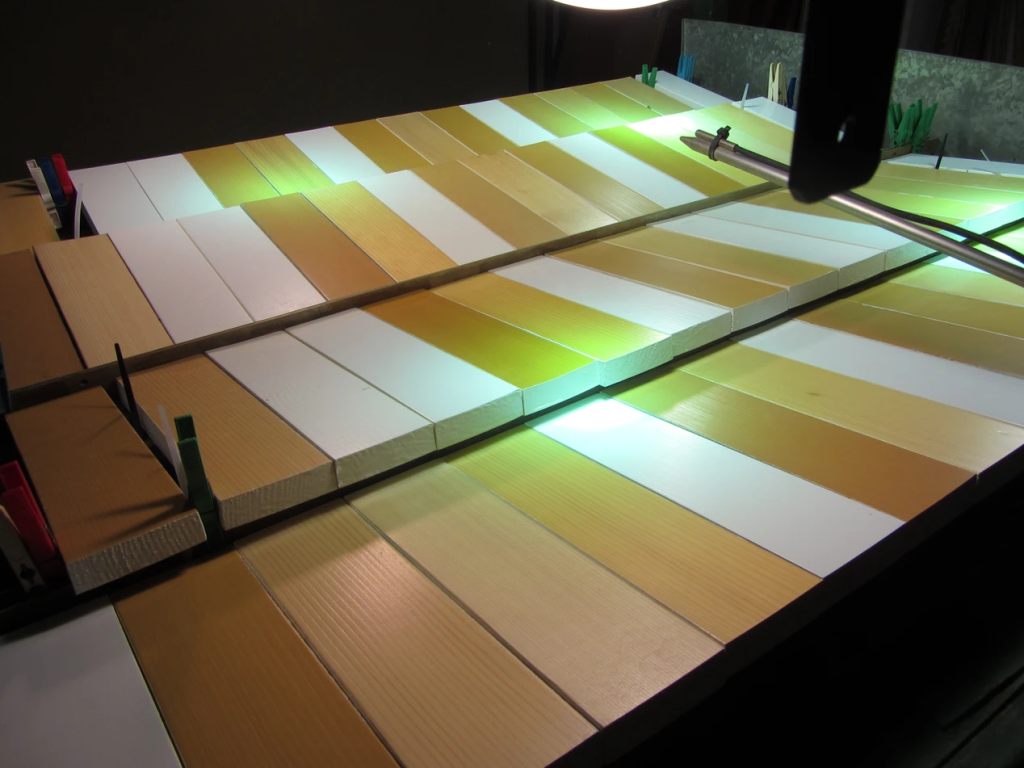
Figure 2: Accelerated ageing of coated wood samples
Based on the results of the analyses carried out in collaboration with University of Ljubljana (Biotechnical faculty, Department of wood science and technology), it has been shown that the thickness of the “lasure” coatings (thickness of the dry film) varied up to 100 % (the minimum measured thickness was 69 μm and the maximum thickness was 136 μm), whereas the thickness of the “opaque” coatings varied up to 51 % (minimum measured thickness of 102 μm and maximum thickness of 155 μm) (Figure 3). Both of these data show great differences between the different producers and between the both types, “lasure” and “opaque” coatings. Since the initial thickness of the coating is not the only important factor affecting the lifetime of the coating, samples have been exposed to 1,000 hours of artificiall accelerated ageing, which corresponds to about 2-3 years of natural aging (Figure 2). The thickness of the coating was measured once again after the accelerated ageing. It was found that the differences in the thickness of the “lasure” and “opaque” coatings after the accelerated ageing process still varied up to 89 % (the minimum thickness of 65 μm and the maximum thickness of 122 μm) and 63 % (the minimum thickness of 86 μm and the maximum thickness of 140 μm) respectively. Even more important was the finding that the intensity of coating thinning varies between manufacturers from 6 % (69 μm to 65 μm) to 40 % (102 μm to 61 μm) in case of »lasure» coatings and from 2 % (122 μm to 119 μm) to 21 % (147 μm to 115 μm) in case of “opaque” coatings. On the basis of the results, it can theoretically be estimated that coating no. 1, which had the lowest initial thickness of the coating, would be sufficient for its entire lifetime (e.g. 30 years) due to its good durability, whereas coating no. 6 needs to be re-painted for the first time after just over 6 years. It is also obvious that the “opaque” coatings are more durable, which results from a different composition and a significantly higher content of pigments.
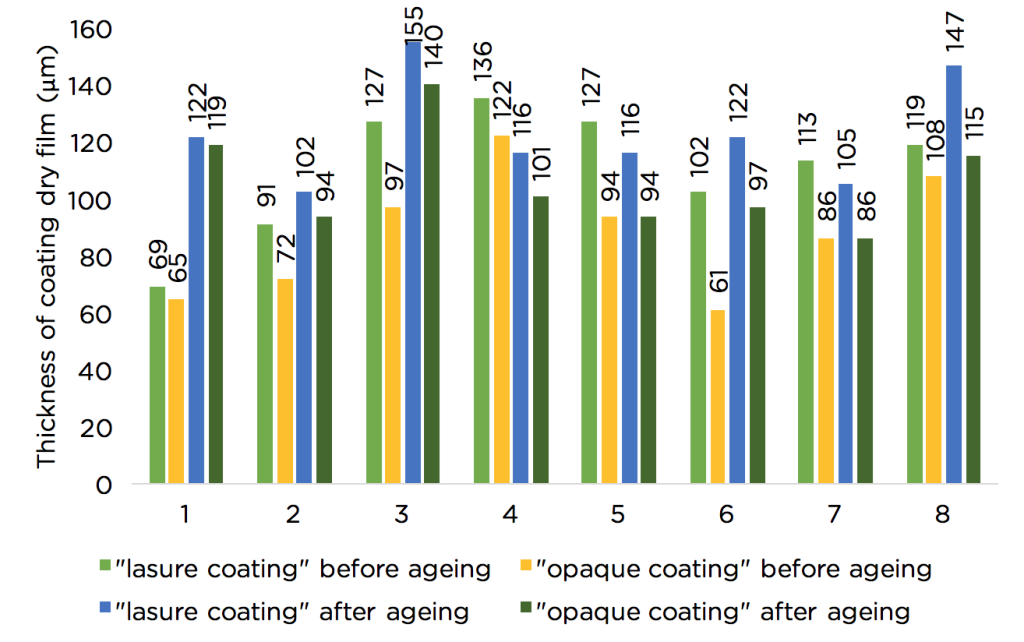
Figure 3: Dry film thickness of »lasure« and »opaque« coating before and after 1,000 hours accelerated ageing
UV radiation is not the only factor affecting the life of the coating and also the wooden windows. Hail is an increasingly present phenomenon, which causes great damage to objects, and also wooden windows, as well as of other materials (e.g. PVC), are often damaged. The correct ratio between elasticity and hardness and the quality of the coating components itself are crucial for the resistance of the coating against hail. In a series of impact resistance tests (a drop of a ball or a hail simulation) it turned out that all the coatings, with an exception of one, were appropriate. Only one of the coatings turned out to be too fragile and cracked after the hit of small ball (Figure 4).
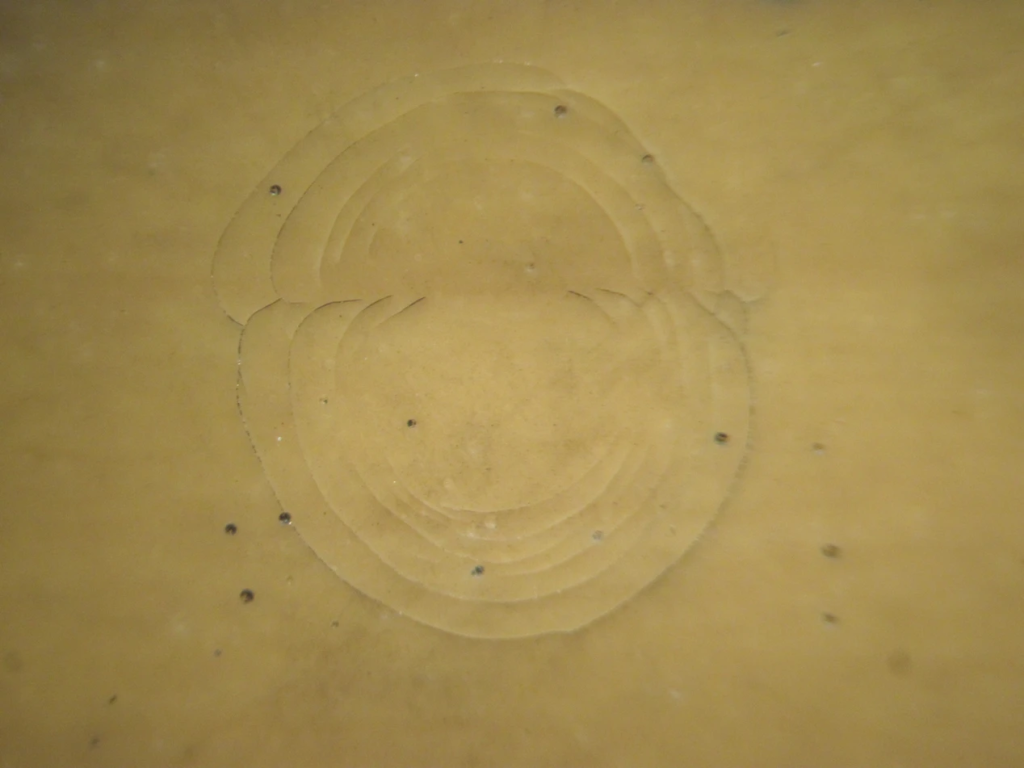
Figure 4: Possible consequence of hail
In case of such a strong impact of hail ice balls that the coating cracks, discolouring soon appears under the coating itself. A reason for this is a penetration of water through the microcracks under the coating and inability of wood to dry fast enough due to general waterproofing of the coating. This results in dark discolouration (Figure 5) and possible peel-off of the coating in the following steps. In the case of hail damage, there is a need for immediate reparation of the coating, with the complete removal of the existing coating and application of a new coating to the clean wooden surface. Certain producers of coatings for wooden windows already intensively develop coatings either with the so-called self-healing technology by incorporation of microcapsules into the coating itself, or ensuring a permanent elasticity of the coating system that provides better resistance to hail and reduces the formation of micro cracks or by ensuring the formation of a low foam surface.
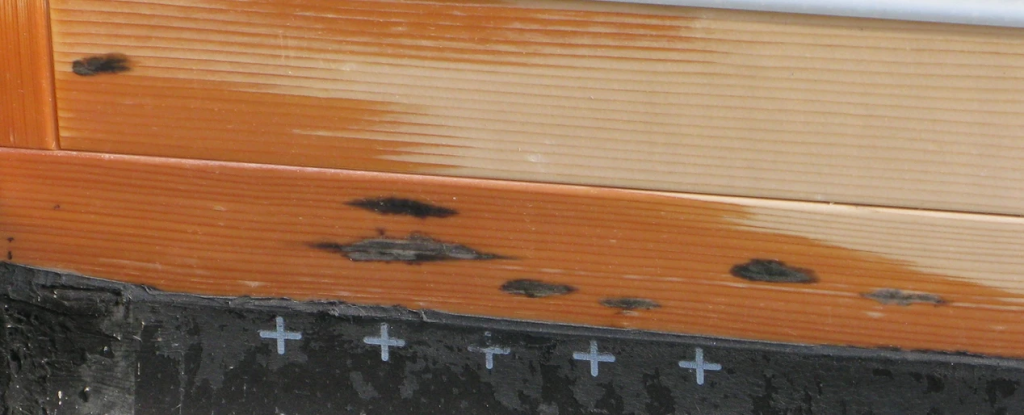
Figure 5: Discolourment under the coating as a consequence of microcracks due to the hail
2. Exposure of wooden windows to rain and solar irradiation
In addition to the quality of the coating, the exposure of the wooden windows at the building is also a key factor affecting the lifetime of the coating and consequently of the wooden window. There is a big difference between the window on the north and south side of the building, and between the windows built in a modern, flat-roofed building with no overhang and a classic building with a 70 cm roof overhang. The sides of the building are unequally exposed to sunlight irradiation, which is well presented at two real cases in the bachelor thesis with a topic about the economic fluctuations at the installation of a solar power plant, where the annual solar radiation on the southern side of the building 1 was 56 % higher than on the northern side, and the 23 % higher in case of object 2. Even bigger effect has the roof overhang, since the windows under it or under the balcony are significantly less exposed to UV irradiation and also protected against hail for most of the year compared to buildings without balconies and overhangs (Figure 6).
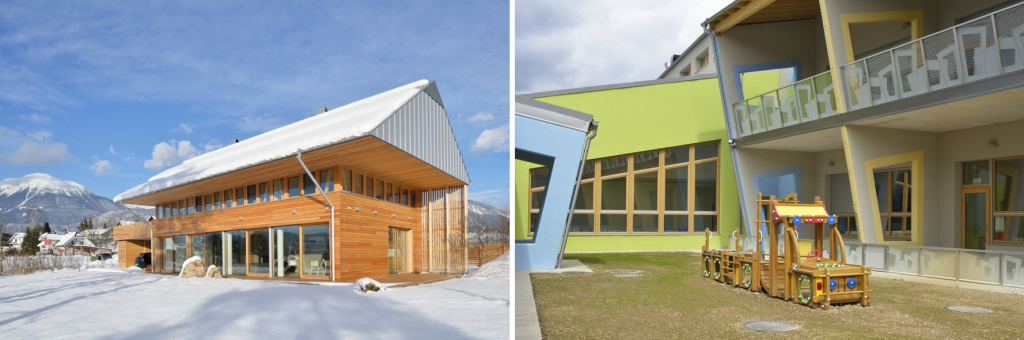
Figure 6: Example of wooden windows protected by a roof or balcony and wooden windows exposed to weather conditions
3. Wooden window details
In the case of wooden windows, however, we should not forget their specific details. The most exposed parts of wooden windows are the lower horizontal window frame and especially scantling. A part of scantling where vertical surface changes to more horizontal part is the most exposed to weather conditions and the coating thickness is the lowest there. Here it is almost necessary to install aluminium covers (Figure 7), which protect these parts from the extensive deterioration of the coating. In addition, the edges exposed to external weather conditions must be rounded in radius of at least 2 mm, thus ensuring as much as possible equal thickness of the coating over the entire surface.
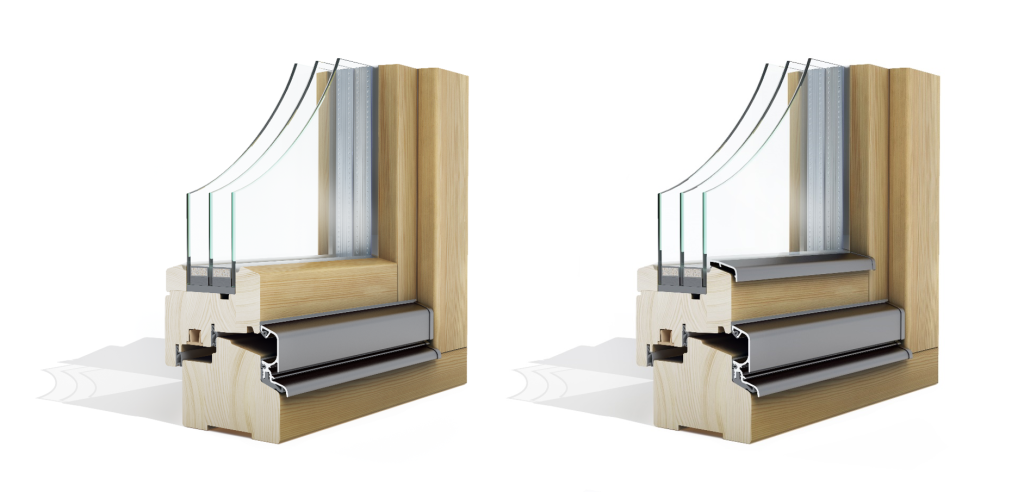
Figure 7: Wooden window without (left) and with water drain cover on casement (right)
After how many years is it necessary to re-paint new wooden window? This is a question at which is, due to all reasons addressed in this paper, difficult to answer precisely. However, it is quite certain that you will re-paint wooden windows much later than it is generally believed, if this will be necessary at all. At normal exposure, use a high-quality coating and its proper application, and assumption that windows won´t be damaged by the hail, there is no need for concern for at least first 15 years.