3D printing represents a term used to define various processes in which material is joined or solidified under computer control to create a three-dimensionalobject. 3D printing has found significant application in both rapid prototypingand additive manufacturing in recent years. Objects can be of almost any shape or geometry and typically are produced using 3D CAD model.
Due to high demand for personalisation and modification in the window industry required by each costumer a serial production of a specific components would not be economically profitable. Production of a single plastic components requires special moulds, tools and machines which cost can easily exceed tens of thousands of €. With advance in the materials and technology used in 3D printing in the resent years it has become possible to 3D print a specifically designed small series (1-10 pieces) with a focus on individual customer requirements and demands.
First step in the design process represents a development of a 3D CAD model. Models are converted in to a STL- “stereolithography” file format. This means that all of the surfaces presented on a model are transformed in to complex combination of the triangular surfaces. STL models are than sliced in to layers in which a 3D printer is capable to produce part. Last step represents the 3D printing process itself.
3D printed parts are physically tested and inspected, and depending to a complexity and requirements remodelling of a CAD files as well as a printing of a new designs can be done couple of times back and forward.
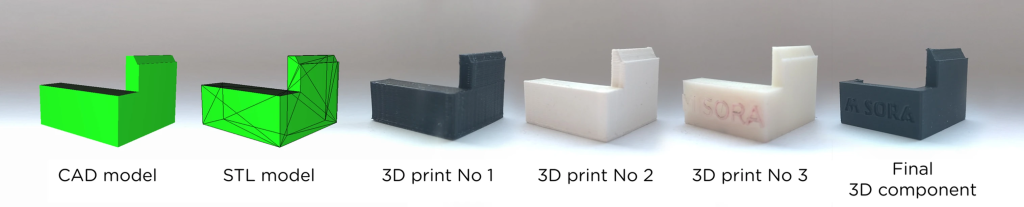
FIG1. Example of the development process, from cad model to final 3D printed component
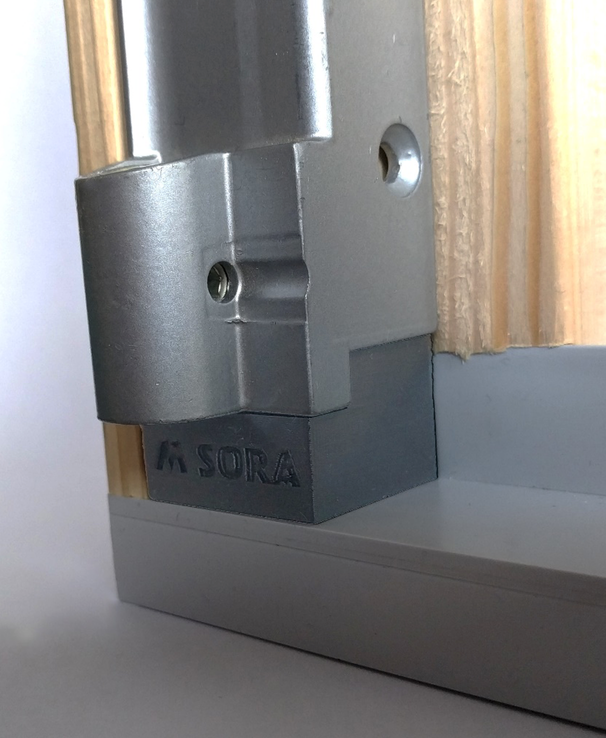
FIG2. Application of final 3D printed component